27 Dec A [Supply] Chain Reaction
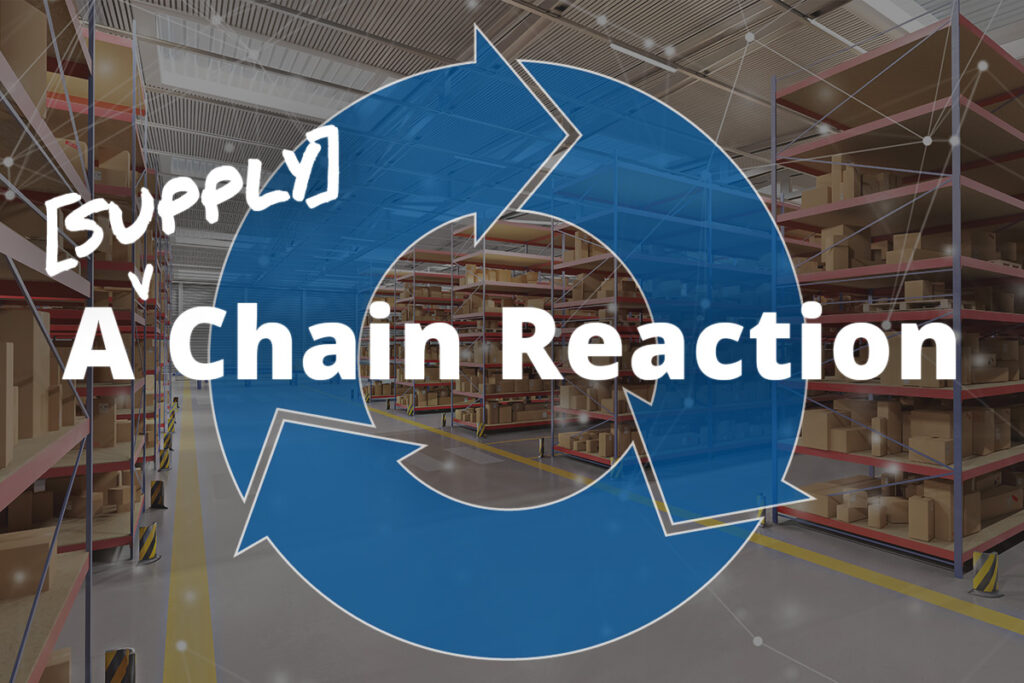
As we rapidly approach the turn of the year, we inch closer to the anniversary of COVID-19’s worldwide debut. Although the passing of time has helped to ease some of the initial discomfort felt, there are still a number of daily challenges that we face as a result of the delayed adaptation of the production and distribution industries. On an international level, we’re experiencing an overly-strained supply chain—shipping delays and material shortages have become standard. Here on Delmarva, we’ve seen the result firsthand, starting with the toilet paper aisle at the grocery store.
When thinking of the supply chain in terms of construction, it’s important to consider our country’s reliance on China, the world’s largest supplier of raw building materials. When faced with the inability to promptly source things like steel, millwork, and plumbing and electrical fixtures, domestic contractors often times feel pinched by their project completion timelines and budgets.
As a solution-oriented construction and development firm, our primary goal has been to maintain resiliency in wake of COVID. Project Manager Robin Steininger recently put these words into action while managing an affordable housing renovation in Georgetown, Delaware.
With demolition already underway, the contracted appliance distributor revealed that they would be unable to fulfill the order due to supply chain hiccups. After contacting the manufacturer, GE, and realizing the depth of the issue, Steininger began the search for a local alternative. With construction schedule deadlines to meet, there was no time to waste.
“Given that this was an affordable housing build, my client had concrete deadlines to meet in order to receive tax credits and funding from lenders. I simply did not have the luxury of asking for more time. I stepped up my game and called the Delaware State Housing Authority for some insight. Understanding what other general contractors were doing to combat these issues was key. From there, I was connected with a Wilmington-based distributor who helped to secure part of our order. The remainder was purchased locally, here in Salisbury,” said Steininger.
Unfortunately, locating the appliances was just the beginning. An overwhelming demand for a very limited inventory presented Robin with yet another hurdle… although the project was still in the demolition phase, she was faced with a choice—purchase now or risk losing out.
“I wound up finding the 150 stoves I needed in order to deliver the apartments on time,” said Steininger. “I had to buy them immediately or they would disappear. Typically, the appliances would be delivered and installed near the end of a project sequence, but with these buildings in the initial demolition phase, that wasn’t an option. Gillis Gilkerson wound up renting a storage unit which allowed me to make the purchase and secure the appliances for our client.”
Robin demonstrated an ability to creatively source local solutions to the national challenges brought on by COVID-related supply chain inconsistencies. Ultimately, her persistence enabled our team to deliver.
In addition to delays, supply and demand challenges have naturally dictated an increase in material costs; a prime example being lumber. The days of using a single supplier are gone with contractors now being forced to shop around in order to fulfill their overall needs. With the residential construction market on fire, demand for lumber is at an all-time high. To put it in perspective, the cost per board-foot has risen from $0.30 in April 2020 to an astounding $0.93 in August— an increase of over 200% in just four months.
Maintaining open lines of communication with teammates, clients, and subcontractors is more important now than ever before. Proactively looking into the future to predict and solve issues before they arise is key, and even the smallest of details cannot be overlooked.
When thinking of the supply chain in terms of construction, it’s important to consider our country’s reliance on China, the world’s largest supplier of raw building materials. When faced with the inability to promptly source things like steel, millwork, and plumbing and electrical fixtures, domestic contractors often times feel pinched by their project completion timelines and budgets.
As a solution-oriented construction and development firm, our primary goal has been to maintain resiliency in wake of COVID. Project Manager Robin Steininger recently put these words into action while managing an affordable housing renovation in Georgetown, Delaware.
With demolition already underway, the contracted appliance distributor revealed that they would be unable to fulfill the order due to supply chain hiccups. After contacting the manufacturer, GE, and realizing the depth of the issue, Steininger began the search for a local alternative. With construction schedule deadlines to meet, there was no time to waste.
“Given that this was an affordable housing build, my client had concrete deadlines to meet in order to receive tax credits and funding from lenders. I simply did not have the luxury of asking for more time. I stepped up my game and called the Delaware State Housing Authority for some insight. Understanding what other general contractors were doing to combat these issues was key. From there, I was connected with a Wilmington-based distributor who helped to secure part of our order. The remainder was purchased locally, here in Salisbury,” said Steininger.
Unfortunately, locating the appliances was just the beginning. An overwhelming demand for a very limited inventory presented Robin with yet another hurdle… although the project was still in the demolition phase, she was faced with a choice—purchase now or risk losing out.
“I wound up finding the 150 stoves I needed in order to deliver the apartments on time,” said Steininger. “I had to buy them immediately or they would disappear. Typically, the appliances would be delivered and installed near the end of a project sequence, but with these buildings in the initial demolition phase, that wasn’t an option. Gillis Gilkerson wound up renting a storage unit which allowed me to make the purchase and secure the appliances for our client.”
Robin demonstrated an ability to creatively source local solutions to the national challenges brought on by COVID-related supply chain inconsistencies. Ultimately, her persistence enabled our team to deliver.
In addition to delays, supply and demand challenges have naturally dictated an increase in material costs; a prime example being lumber. The days of using a single supplier are gone with contractors now being forced to shop around in order to fulfill their overall needs. With the residential construction market on fire, demand for lumber is at an all-time high. To put it in perspective, the cost per board-foot has risen from $0.30 in April 2020 to an astounding $0.93 in August— an increase of over 200% in just four months.
Maintaining open lines of communication with teammates, clients, and subcontractors is more important now than ever before. Proactively looking into the future to predict and solve issues before they arise is key, and even the smallest of details cannot be overlooked.